Selecting the perfect storage racking system for your warehouse isn’t just about buying shelves—it’s a strategic decision that impacts efficiency, safety, and profitability. With options ranging from selective pallet racks to high-density automated systems, the wrong choice can lead to wasted space, slower workflows, and even workplace hazards. In this comprehensive guide, we’ll walk you through the key factors to consider, compare popular storage racking types, and share actionable tips to ensure your warehouse operates at peak performance.
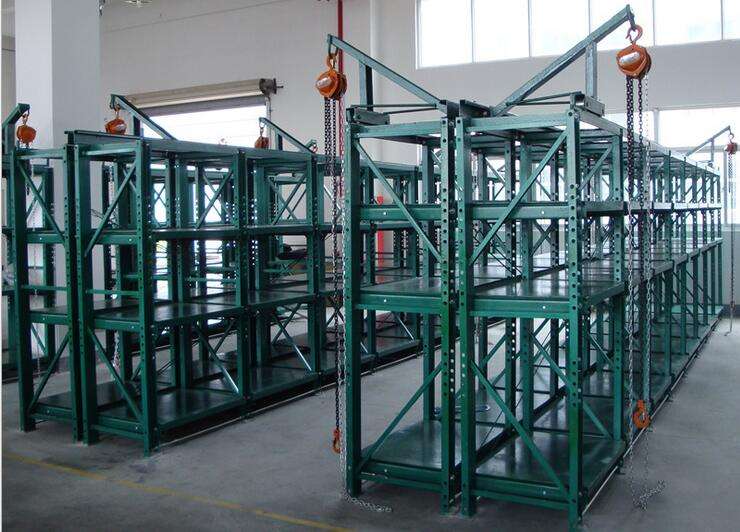
Why Your Storage Racking Choice Matters
Your storage racking system is the backbone of your warehouse. It directly affects:
- Space Utilization: Maximizing vertical and horizontal storage capacity.
- Operational Efficiency: Reducing pick times, labor costs, and errors.
- Safety: Preventing collapses, overloading, or aisle congestion.
- Scalability: Adapting to seasonal demand or business growth.
A well-chosen system can boost productivity by 20–40%, while a poor fit can drain resources. Let’s dive into how to make the right choice.
Step 1: Assess Your Warehouse Needs
A. Understand Your Inventory
- Product Types: Are you storing pallets, small parts, or mixed sizes?Example: Automotive parts may require bin shelving, while bulk pallets need heavy-duty racks.
- Weight and Dimensions: Calculate maximum load per shelf (e.g., 500 lbs vs. 10,000 lbs).
- Turnover Rates: Prioritize quick access for high-demand SKUs (A-items) and dense storage for slow movers (C-items).
B. Audit Your Space
- Ceiling Height: Warehouses with 30+ ft ceilings can leverage vertical storage racking like cantilever or mezzanine systems.
- Floor Strength: Older facilities may need reinforcement for heavy loads.
- Aisle Width: Match to equipment (e.g., 8–10 ft for narrow-aisle forklifts).
C. Plan for Growth
- Will you expand inventory by 20% in 3 years?
- Are automation or robotics part of your future roadmap?
Step 2: Compare Storage Racking Types
- Best For: High-SKU diversity with frequent access needs.
- Features: Adjustable beams, direct pallet access.
- Pros: Affordable, flexible, easy to install.
- Cons: Requires wide aisles (10–13 ft) for forklifts.
- Best For: Bulk storage of identical products (e.g., beverages, paper goods).
- Features: Forklifts drive into lanes to store pallets 5–10+ deep.
- Pros: Maximizes space (50–75% denser than selective racks).
- Cons: Limited SKU variety; higher risk of product damage.
3. Push Back Racking
- Best For: Medium-turnover goods needing a balance of density and accessibility.
- Features: Pallets ride on inclined carts; last-in, first-out (LIFO) system.
- Pros: Stores 2–6 pallets deep without forklift entry.
- Cons: Higher cost per pallet position.
- Best For: High-speed picking of small cases (e-commerce, pharmaceuticals).
- Features: Gravity rollers move cartons forward automatically.
- Pros: Cuts picking time by 50%+ with FIFO flow.
- Cons: Requires uniform box sizes.
5. Mobile Aisle Racking
- Best For: Space-constrained warehouses or cold storage.
- Features: Shelves on tracks create on-demand aisles.
- Pros: Doubles storage capacity.
- Cons: Slower access; higher upfront cost.
Step 3: Prioritize Safety and Compliance
A. Weight Limits and Load Distribution
- Never exceed the rack’s rated capacity.
- Distribute weight evenly to prevent tipping.
B. OSHA and Local Regulations
- Aisle Widths: 36” minimum for pedestrian zones; 8–13 ft for equipment.
- Anchoring: Secure racks to floors in seismic zones.
C. Anti-Collapse Features
- Install safety pins, cross braces, or mesh decking.
- Use column protectors to guard against forklift impacts.
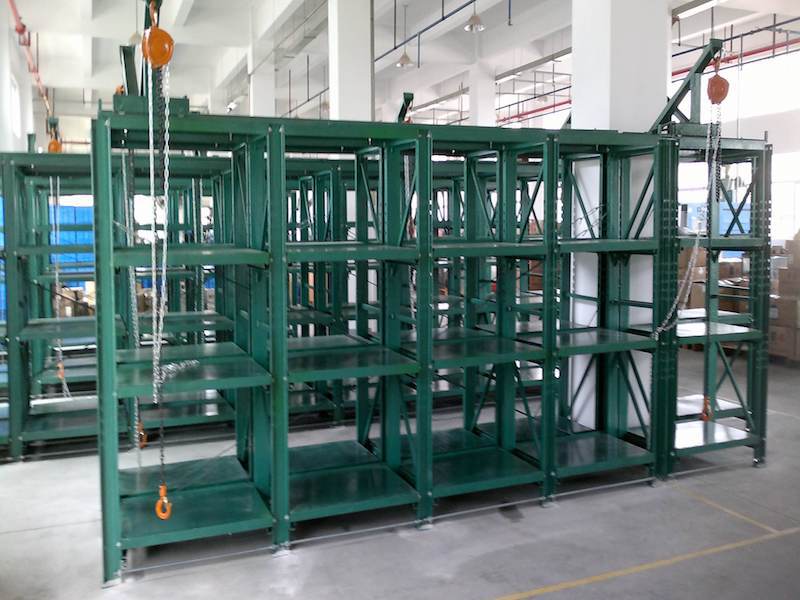
Step 4: Calculate Costs and ROI
A. Upfront Costs
- Racking: 50–50–500 per pallet position (varies by type).
- Installation: 1,000–1,000–10,000+ for complex systems.
- Permits: Required for mezzanines or high-density setups.
B. Hidden Costs
- Maintenance: Inspections, part replacements, and lubrication.
- Training: Operators need to learn new systems (e.g., push back racks).
C. ROI Factors
- Labor Savings: Faster picking = lower payroll costs.
- Space Savings: Delay costly expansions with higher density.
- Damage Reduction: Proper racks prevent product losses.
Step 5: Test Before Committing
A. Request Demos or Samples
- Test load capacity with your heaviest items.
- Check ease of assembly/disassembly.
B. Pilot Programs
- Install a small section first to gauge workflow impact.
C. Consult Experts
- Work with warehouse planners or engineers for tailored layouts.
Case Study: How a 3PL Warehouse Boosted Efficiency by 35%
- Problem: A logistics company faced 25% mispick rates and wasted 30% of floor space.
- Solution: They implemented selective racks for fast movers and carton flow racks for small items.
- Result: Picking speed increased by 35%, and storage capacity grew by 40%.
Future Trends in Storage Racking
- Automation Integration: AMRs (robots) and AS/RS (automated systems) for high-density warehouses.
- Sustainable Materials: Recycled steel racks and energy-efficient designs.
- Smart Racking: IoT sensors to monitor load weight, humidity, or structural stress.
Final Checklist for Choosing Storage Racking
- Audited inventory type, weight, and turnover rates.
- Measured warehouse dimensions (height, floor strength, column spacing).
- Compared quotes from 3+ suppliers.
- Ensured compliance with OSHA and local codes.
- Planned for future automation or expansion.
How to Choose the Right Storage Racking for Your Warehouse
The right storage racking system transforms chaos into order, slashing costs and supercharging productivity. By aligning your choice with inventory needs, space constraints, and growth goals, you’ll build a warehouse that’s efficient, safe, and ready for the future. Don’t just store—optimize.