Selecting the right warehouse shelves isn’t just about storage—it’s about unlocking efficiency, safety, and scalability for your business. With countless options on the market, from boltless shelving to industrial pallet racks, the wrong choice can lead to wasted space, higher costs, and even workplace accidents. In this guide, we’ll break down the key factors to consider, compare popular shelving types, and share pro tips to ensure your investment pays off for years to come.
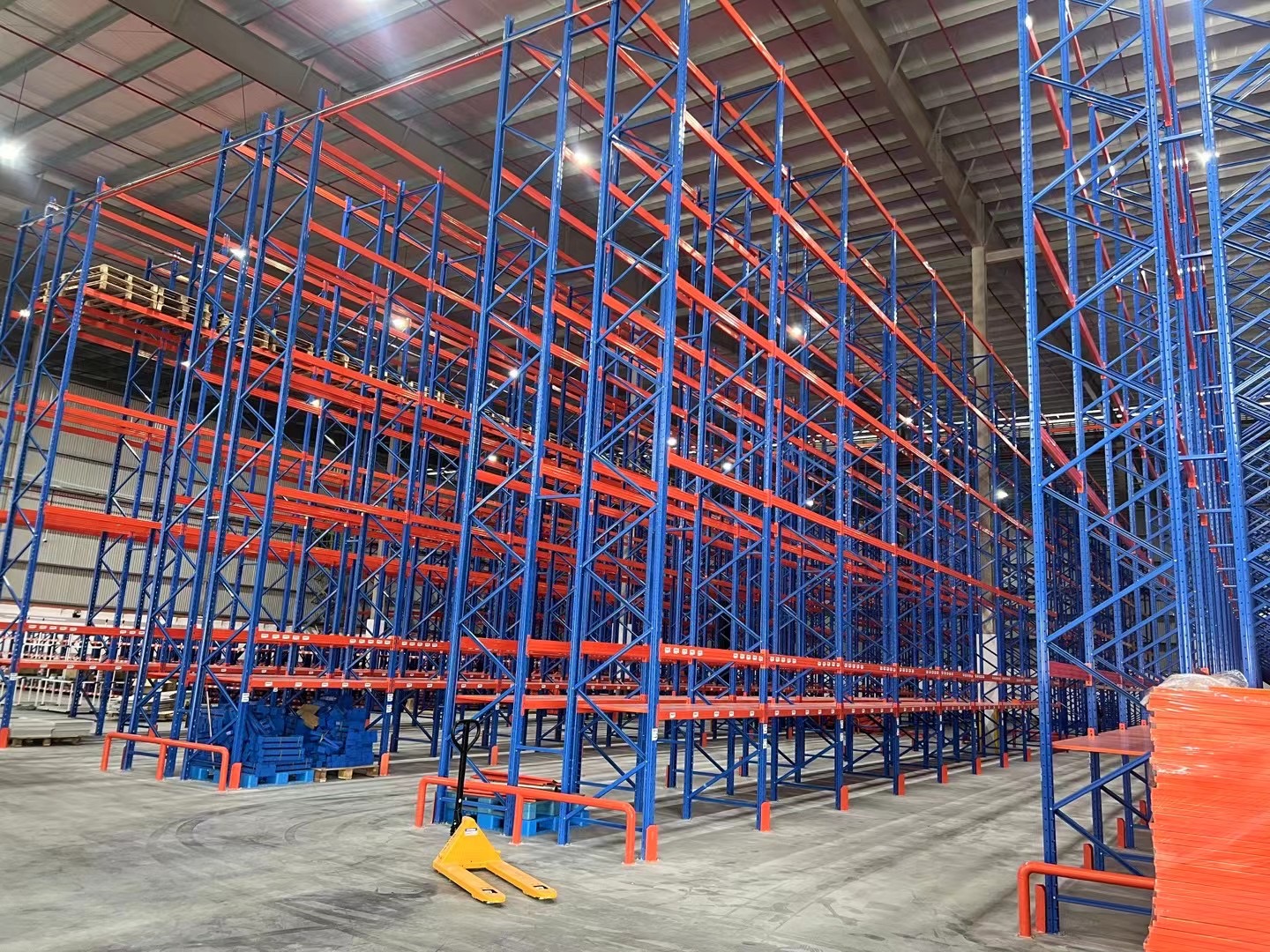
Why Your Warehouse Shelves Matter More Than You Think
Warehouse shelves are the backbone of your operation. They influence:
- Space Utilization: Maximizing vertical and horizontal storage capacity.
- Workflow Efficiency: Reducing pick times and labor costs.
- Safety: Preventing collapses, spills, or overloading risks.
- Scalability: Adapting to seasonal demand or business growth.
A poorly chosen system can drain 15–30% of productivity. Let’s fix that.
Step 1: Assess Your Storage Needs
A. Inventory Analysis
- SKU Types: Are you storing small parts, boxes, pallets, or oversized items?Example: Automotive parts require bin shelving, while bulk pallets need heavy-duty racks.
- Turnover Rate: High-turnover items should be placed in easily accessible “golden zones.”
- Weight Requirements: Calculate maximum load per shelf (e.g., 500 lbs vs. 5,000 lbs).
B. Space Audit
- Measure ceiling height, floor space, and aisle width.
- Identify obstructions (columns, doors, HVAC systems).
- Use CAD software or consult a warehouse planner for 3D layout simulations.
C. Future-Proofing
- Will your inventory grow by 20% in 5 years?
- Are you planning to automate (e.g., robotics or conveyor integration)?
Step 2: Compare Types of Warehouse Shelves
1. Selective Pallet Racking
- Best For: High-SKU diversity with frequent access.
- Features: Adjustable beams, easy forklift access.
- Load Capacity: Up to 3,000 lbs per shelf.
- Pros: Flexible, cost-effective.
- Cons: Requires wider aisles for forklifts.
2. Cantilever Shelving
- Best For: Long, bulky items (pipes, lumber, furniture).
- Features: Arms extend from vertical columns, no front obstructions.
- Load Capacity: Up to 10,000 lbs per arm.
- Pros: Ideal for irregular shapes.
- Cons: Not suited for small items.
3. Wire Shelving
- Best For: Small parts, retail stockrooms, or cold storage.
- Features: Ventilated design, corrosion-resistant.
- Load Capacity: 200–800 lbs per shelf.
- Pros: Easy to clean, prevents dust buildup.
- Cons: Not ideal for heavy pallets.
4. Mobile Aisle Shelving (Compact Shelving)
- Best For: Space-starved warehouses.
- Features: Shelves on tracks, moved via hand crank or motor.
- Load Capacity: 1,000–2,500 lbs per shelf.
- Pros: Doubles storage density.
- Cons: Higher upfront cost.
5. Mezzanine Shelving
- Best For: Adding multi-level storage without expanding footprint.
- Features: Platform structures with integrated shelves.
- Load Capacity: Varies by design (up to 300 lbs/sq ft).
- Pros: Utilizes vertical space.
- Cons: Requires reinforced flooring.
Step 3: Prioritize Safety and Compliance
A. Weight Limits
- Never exceed the manufacturer’s load rating.
- Distribute weight evenly to prevent tipping.
B. Seismic and OSHA Standards
- In earthquake-prone areas, anchor shelves to floors/walls.
- Follow OSHA guidelines for aisle width (e.g., 36” minimum for pedestrian zones).
C. Anti-Collapse Features
- Install safety pins, cross braces, or mesh decking.
- Use column guards to protect against forklift impacts.
Step 4: Calculate Costs and ROI
A. Upfront Costs
- Shelving Units: 50–50–500 per section.
- Installation: 200–200–1,000+ (varies by complexity).
- Permits: Required for mezzanines or high-density systems.
B. Hidden Costs
- Maintenance (e.g., beam replacement, lubrication).
- Labor retraining for new systems.
C. ROI Factors
- Reduced labor hours (e.g., faster picking).
- Lower storage costs per square foot.
- Fewer product damages or accidents.
Step 5: Test Before You Invest
A. Request Samples
- Test load capacity with your heaviest items.
- Check ease of assembly/disassembly.
B. Visit Showrooms
- See systems in action (e.g., how forklifts interact with pallet racks).
C. Pilot Programs
- Install a small section first to gauge workflow impact.
Case Study: How XYZ Logistics Boosted Efficiency by 40%
- Problem: A 50,000 sq ft warehouse struggled with chaotic storage and 25% mispick rates.
- Solution: They switched from static shelving to warehouse shelves with carton flow racks for high-turnover items and added a mezzanine for seasonal stock.
- Result: Picking speed increased by 40%, and storage capacity grew by 60%.
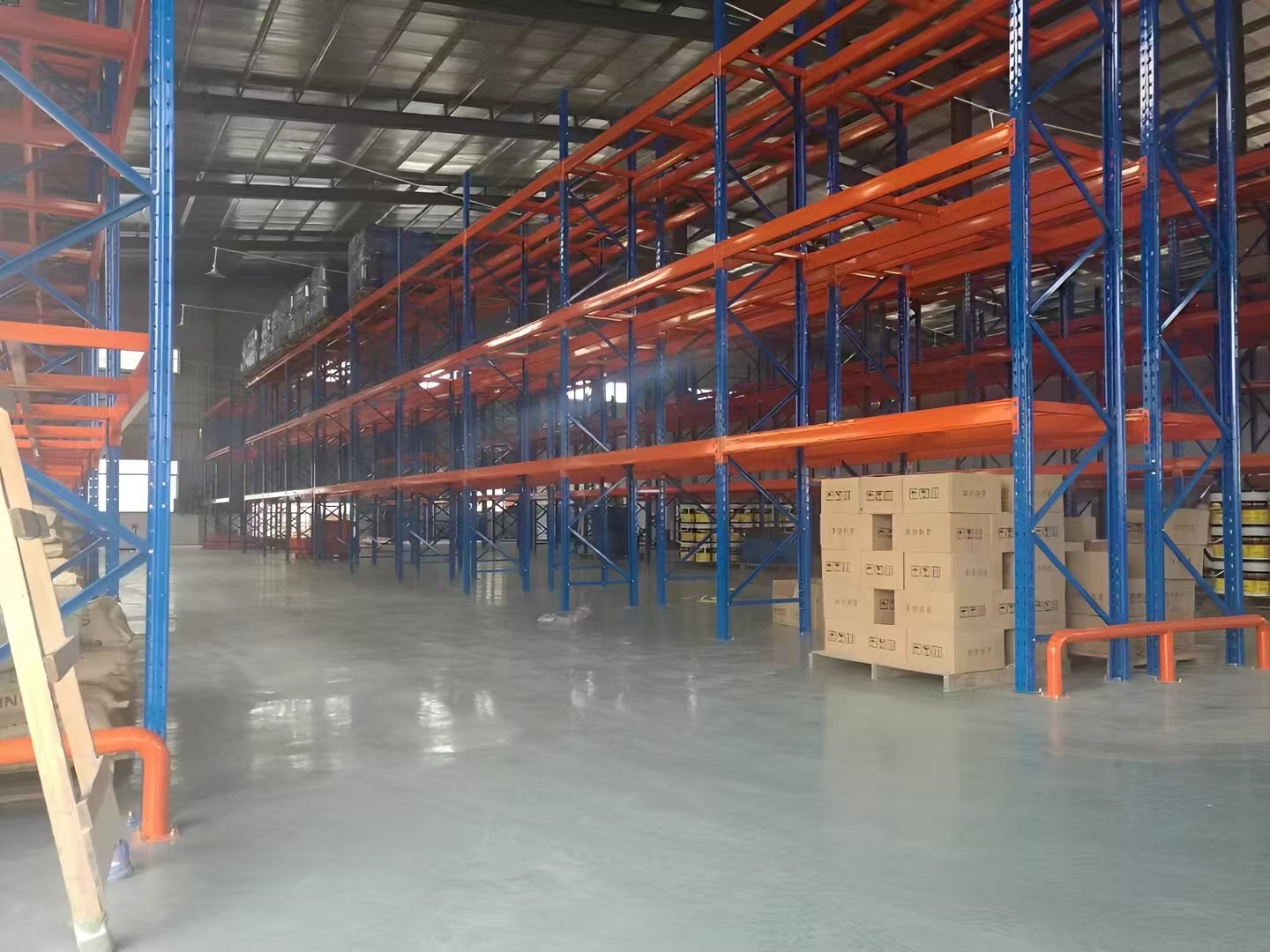
Future Trends in Warehouse Shelving
- AI-Driven Layouts: Systems that auto-adjust shelving positions based on real-time demand.
- Sustainable Materials: Recycled steel or bamboo shelving.
- IoT Sensors: Monitor load weight, humidity, or structural stress.
Final Checklist Before Buying Warehouse Shelves
- Confirmed load requirements (current + future).
- Measured warehouse dimensions (height, floor plan).
- Compared quotes from 3+ suppliers.
- Checked compliance with local building codes.
- Planned for tech integrations (WMS, automation).
How to Choose the Best Warehouse Shelves for Your Business
The right warehouse shelves can transform chaos into order, cutting costs and supercharging productivity. By matching your inventory needs, space constraints, and growth goals to the perfect system, you’ll build a warehouse that works smarter—not harder.