Your storage racking system is more than just metal beams and shelves—it’s a critical asset that keeps your warehouse running smoothly. Neglect it, and you risk costly collapses, OSHA violations, and operational downtime. But with regular maintenance, your racks can last decades, protect your inventory, and keep your team safe. In this guide, we’ll share actionable tips to extend the life of your storage racking, spot early warning signs of damage, and avoid the $100,000+ costs of system failure.
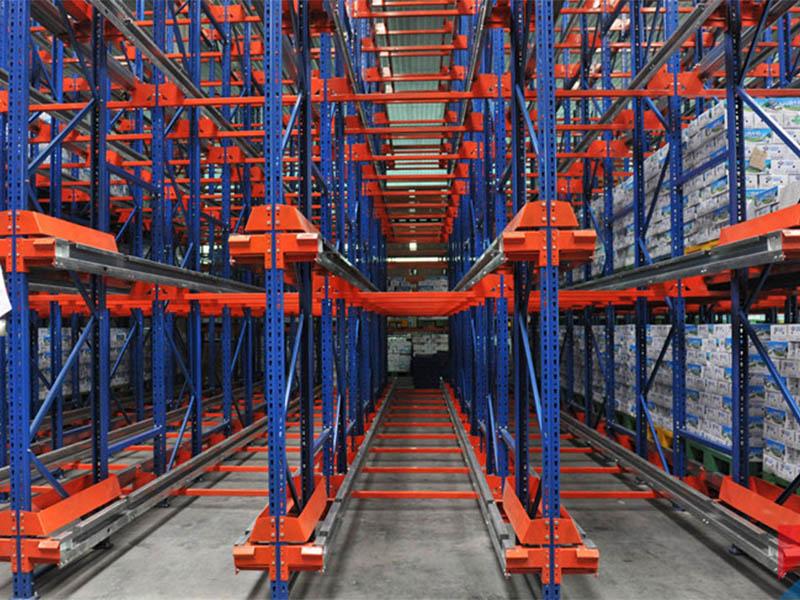
Why Storage Racking Maintenance Matters
A single damaged beam or loose anchor can trigger a domino effect. Consider these stats:
- 85% of racking failures stem from improper use or lack of inspections.
- The average cost of a storage racking collapse exceeds $500,000 in lost inventory, fines, and downtime.
- OSHA penalties for unsafe racks can reach $15,625 per violation.
Proactive maintenance isn’t just smart—it’s non-negotiable.
8 Essential Storage Racking Maintenance Tips
1. Conduct Regular Inspections
Frequency: Weekly visual checks + annual professional audits.
What to Look For:
- Bent or Twisted Uprights: Even a 1/4-inch bend can compromise structural integrity.
- Cracked Welds: Common at beam-to-upright connections.
- Loose Anchors: Check floor bolts for rust or separation.
- Dented Beams: Caused by forklift impacts.
Pro Tip: Use a checklist aligned with ANSI MH16.1 or FEM 10.2.02 standards.
2. Enforce Load Capacity Limits
Overloading is the #1 cause of storage racking failures.
- Calculate Safe Loads: Include the weight of pallets, containers, and the rack itself.
- Label Clearly: Post max load limits on each beam (e.g., “2,500 lbs per shelf”).
- Distribute Weight Evenly: Avoid placing heavy items on one side of a pallet.
Case Study: A Midwest distributor reduced beam stress by 40% after training staff on balanced loading.
3. Protect Against Forklift Damage
Forklifts account for 60% of rack damage. Mitigate risks with:
- Column Guards: Steel protectors around uprights.
- Aisle Markers: Reflective tape or LED lights to guide operators.
- Speed Limits: Enforce 5 mph max in rack zones.
Pro Tip: Install impact sensors that alert managers to collisions in real time.
4. Keep Floors Level and Clean
Uneven floors shift weight unevenly, warping racks over time.
- Check Floor Flatness: Use a laser level; gaps >1/8 inch per foot need correction.
- Clean Spills Immediately: Oil or water accelerates corrosion.
- Repair Cracks: Hire a professional to fix damaged concrete.
5. Address Corrosion and Rust
Moisture, chemicals, and humidity eat away at storage racking.
- Spot Early Signs: Look for bubbling paint or orange discoloration.
- Treat Affected Areas: Sand rusted spots and apply anti-corrosion paint.
- Prevent Future Damage: Use dehumidifiers or coated racks in damp areas.
6. Retighten Bolts and Anchors
Vibration from equipment or seismic activity loosens fasteners.
- Torque Check: Use a torque wrench to ensure bolts meet manufacturer specs (e.g., 50 ft-lbs).
- Replace Worn Parts: Don’t reuse stripped bolts or cracked anchors.
7. Update Labels and Signage
Faded or missing labels lead to misloading and accidents.
- Refresh Labels Quarterly: Include load limits, SKU zones, and hazard warnings.
- Use Color Coding: Red for heavy-duty beams, green for inspected sections.
8. Train Your Team Continuously
Human error causes 70% of racking issues. Train staff on:
- Safe Loading Practices: No climbing, uneven stacking, or exceeding limits.
- Damage Reporting: Empower workers to flag issues immediately.
- Emergency Protocols: What to do if a beam bends or load shifts.
When to Repair vs. Replace Storage Racking
Repair If:
- Damage is isolated (e.g., one bent beam).
- Cost is <30% of replacement.
- The rack meets current safety standards post-repair.
Replace If:
- Uprights are twisted >3 degrees from vertical.
- Multiple beams are cracked or corroded.
- The system no longer meets OSHA or ANSI guidelines.
Pro Tip: Work with a racking engineer for professional assessments.
Advanced Maintenance Tools and Tech
1. Ultrasonic Testing
Detects hidden cracks or weaknesses in welds using sound waves.
2. 3D Laser Scanning
Creates digital models to identify misalignments or stress points.
3. IoT Monitoring
Sensors track load weight, vibration, and temperature in real time.
4. Drone Inspections
Capture high-altitude views of hard-to-reach racks in large warehouses.
Case Study: How a Food Distributor Avoided Catastrophe
The Problem: Routine inspection found a cracked weld in a critical upright supporting 8,000 lbs of frozen goods.
The Solution: They shut down the aisle, replaced the upright, and retrained forklift drivers on collision avoidance.
The Result: Prevented a potential $2M collapse and 3-day shutdown.
Common Maintenance Mistakes to Avoid
- Ignoring “Minor” DamageA small dent can weaken a beam’s load capacity by 20%—fix it ASAP.
- Using Non-Approved PartsOff-brand bolts or beams may not meet safety standards.
- Skipping DocumentationKeep records of inspections, repairs, and training for compliance audits.
Creating a Maintenance Schedule
Task | Frequency | Responsibility |
---|
Visual Inspections | Weekly | Warehouse Manager |
Bolt Tightening | Quarterly | Maintenance Team |
Professional Audit | Annually | Certified Racking Engineer |
Staff Training | Biannually | Safety Officer |
The Cost of Neglect vs. Proactive Care
Factor | No Maintenance | Regular Maintenance |
---|
Lifespan | 5–10 years | 20–30 years |
Annual Repair Costs | 10,000–10,000–50,000 | 2,000–2,000–5,000 |
Collapse Risk | High | Low |
Storage Racking Maintenance Tips for Longevity
Your storage racking system is a long-term investment—treat it like one. By adopting a proactive maintenance routine, you’ll prevent disasters, reduce costs, and ensure your racks support your business for decades. Don’t wait for a crisis; start inspecting, training, and reinforcing today.