When it comes to organizing your warehouse, retail stockroom, or industrial facility, the choice between storage racking and traditional shelving isn’t just about preference—it’s about precision. Each system has unique strengths, costs, and use cases, and picking the wrong one can lead to wasted space, inefficiency, and even safety risks. In this guide, we’ll dissect the differences, compare pros and cons, and help you decide whether storage racking or shelving is the right fit for your operation.
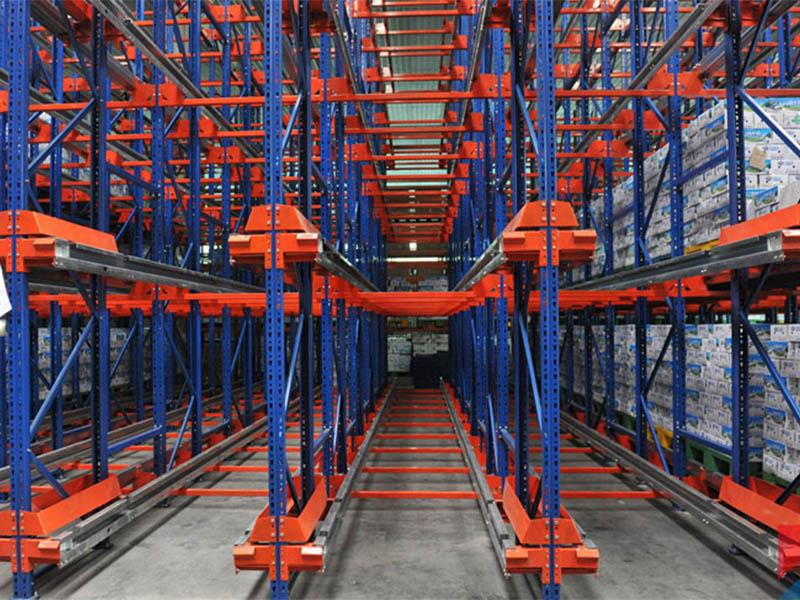
What’s the Difference? Core Definitions
Storage Racking
Storage racking refers to heavy-duty systems designed to store large, bulky, or palletized loads. These structures are engineered for high weight capacities, vertical space utilization, and compatibility with forklifts or other industrial equipment. Common types include:
- Selective Pallet Racks
- Drive-In/Drive-Through Racking
- Cantilever Racking
Shelving
Shelving systems are lighter-duty solutions for smaller, hand-stacked items. They’re typically used for:
- Boxes
- Bin storage
- Retail inventory
- Tools or parts
Key differences lie in weight capacity, accessibility, and scalability.
Head-to-Head Comparison: Storage Racking vs. Shelving
1. Weight Capacity
- Storage Racking: Built for heavy loads—up to 30,000 lbs per pallet position in cantilever systems.
- Shelving: Typically handles 200–2,000 lbs per shelf, depending on material (steel vs. particleboard).
Verdict: Storage racking wins for industrial-scale loads; shelving suits lighter items.
2. Space Efficiency
- Storage Racking: Maximizes vertical space (up to 40+ feet tall) with minimal floor footprint.
- Shelving: Focuses on horizontal organization, ideal for low-ceiling rooms or small stockrooms.
Verdict: Storage racking is better for warehouses with high ceilings; shelving fits compact spaces.
3. Accessibility
- Storage Racking: Designed for forklift access, with options like selective racks (direct access) or push-back systems (LIFO).
- Shelving: Optimized for manual picking, often requiring ladders or step stools.
Verdict: Storage racking supports high-speed, equipment-driven workflows; shelving suits hands-on operations.
4. Cost
- Storage Racking: Higher upfront costs (50–50–500+ per pallet position) but offers long-term ROI via density and durability.
- Shelving: Affordable (20–20–300 per unit) but may require frequent replacements in heavy-use environments.
Verdict: Shelving is budget-friendly for light needs; storage racking pays off for large-scale ops.
5. Flexibility
- Storage Racking: Modular designs allow reconfiguration, but changes often require equipment and labor.
- Shelving: Easily adjusted or moved by hand, ideal for dynamic retail or workshop spaces.
Verdict: Shelving offers day-to-day flexibility; storage racking is better for fixed, high-volume layouts.
When to Choose Storage Racking
1. You Store Palletized Goods
If your inventory arrives on pallets, storage racking is non-negotiable. Shelving can’t safely handle the weight or size of loaded pallets.
2. You Need High-Density Storage
Industries like food distribution, manufacturing, or e-commerce rely on storage racking to store more goods in less space. Drive-in racks, for example, can hold 5–10 pallets deep.
3. You Use Heavy Equipment
Forklifts, order pickers, and pallet jacks require the wide aisles and robust frames that storage racking provides.
4. You Prioritize Long-Term Durability
Steel storage racking systems last decades with minimal maintenance, while shelving may warp or sag under constant heavy use.
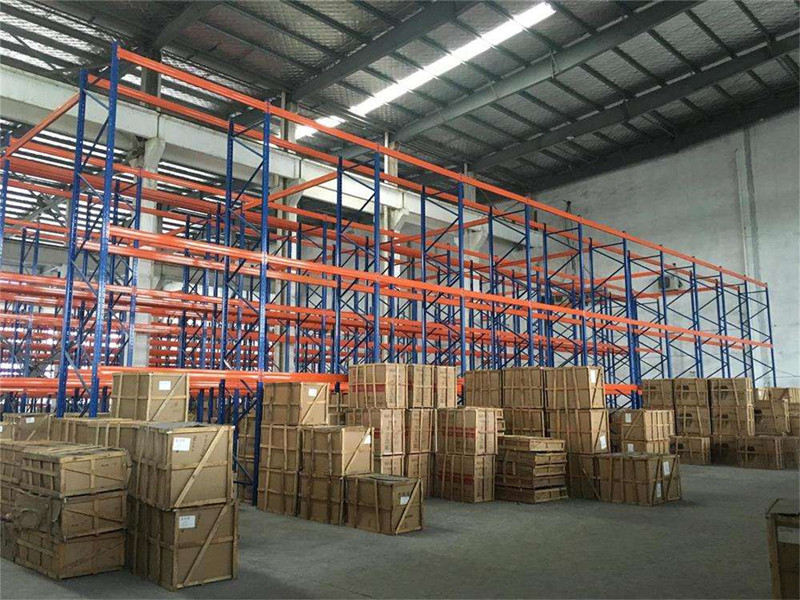
When to Choose Shelving
1. You Handle Small Items or Cartons
Shelving’s bins, drawers, and adjustable shelves are perfect for organizing tools, retail products, or office supplies.
2. You Operate in Tight Spaces
Stockrooms, garages, or boutique warehouses with low ceilings benefit from shelving’s compact, vertical design.
3. You Need Frequent Reconfiguration
Retailers or workshops that rotate inventory seasonally can easily rearrange shelving without heavy machinery.
4. You’re on a Tight Budget
For startups or small businesses, shelving offers a low-cost way to organize without a major upfront investment.
Hybrid Solutions: Blending Storage Racking and Shelving
Many facilities combine both systems for optimal efficiency:
- Use storage racking for bulk pallets of raw materials.
- Install shelving nearby for tools, packaging supplies, or pick-and-pack stations.
Example: An auto parts warehouse uses cantilever racks for long metal pipes and wire shelving for small components like bolts and gaskets.
Cost Analysis: Breaking Down the Numbers
Storage Racking
- Selective Pallet Racks: 100–100–250 per pallet position.
- Installation: 1,000–1,000–5,000+ (depending on size).
- Lifespan: 20–30 years with proper maintenance.
Shelving
- Steel Shelving: 150–150–600 per unit (5–7 shelves).
- Plastic/Wire Shelving: 50–50–300 per unit.
- Lifespan: 5–15 years, depending on load and environment.
Tip: Calculate cost per square foot stored—storage racking often wins for large facilities.
Safety Considerations
Storage Racking Risks
- Overloading: Exceeding weight limits causes collapses.
- Forklift Damage: Impacts can bend uprights; install column guards.
- Poor Anchoring: Unsecured racks tip in seismic zones.
Shelving Risks
- Overcrowding: Uneven weight distribution leads to tipping.
- Climbing: Workers standing on shelves risk falls.
- Low Durability: Cheap materials buckle under heavy loads.
Real-World Case Studies
Case 1: E-Commerce Fulfillment Center
- Challenge: Needed to store 10,000+ SKUs, including both pallets and small items.
- Solution: Installed storage racking for palletized goods and mobile shelving for pick-and-pack zones.
- Result: Reduced picking errors by 25% and doubled storage capacity.
Case 2: Automotive Repair Shop
- Challenge: Limited floor space for tools and spare parts.
- Solution: Used heavy-duty steel shelving for tools and cantilever storage racking for tires and exhaust systems.
- Result: Cut clutter and improved technician productivity by 30%.
Future Trends Impacting Your Choice
- Automation: Storage racking is evolving to integrate with robots and AS/RS (Automated Storage/Retrieval Systems).
- Sustainability: Recycled steel racks and eco-friendly shelving materials (e.g., bamboo) are gaining traction.
- Smart Tech: IoT sensors in storage racking monitor load weight, while RFID tags on shelving track inventory in real time.
How to Decide: A 5-Step Checklist
- Audit Inventory: List item types, sizes, weights, and turnover rates.
- Measure Space: Note ceiling height, floor strength, and aisle requirements.
- Project Growth: Will you scale up or diversify inventory in 3–5 years?
- Budget: Compare upfront costs vs. long-term ROI.
- Test: Run a pilot with a small section of racks or shelves.
Storage Racking vs. Shelving: Which One Fits Your Needs?
The choice between storage racking and shelving boils down to your inventory, space, and workflow. Storage racking dominates in heavy-duty, high-density environments, while shelving shines for small-item flexibility and budget-friendly setups. By aligning your choice with operational needs, you’ll transform storage from a headache into a competitive advantage.